Precision casting generally refers to the process of producing precision-sized castings. Precision casting produces castings with more precise dimensions and a better surface finish than traditional sand casting. Precision, complexity, and close to the final shape of a part are its hallmarks. Direct use without further processing or processing is possible. Near-net-shape is an advanced fabrication method. It can also be used for low-quantity orders.
Investment casting, or lost wax casting, is commonly used for precision casting. It is commonly used to produce ferrous and nonferrous metals.
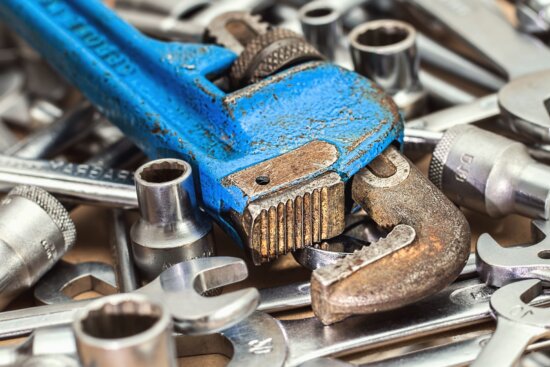
Suitable investment materials, such as paraffin, are used to make the investment mold. On the investment mold, the refractory coating and refractory sand processes are repeated. After the shell has been hardened, it is dried. A cavity is then created by melting off the internal melting mold. The baked shell is then obtained to obtain sufficient strength. Burning off the residual investment material, the desired metal material is poured. It is solidified, cooled, shelled, and sanded. Thus, an extremely precise product is obtained. The surface is treated with heat and cold depending on the requirements of the product.
Furthermore, Precision castings have a great deal of flexibility in their design and materials. Investment castings can be made from different types of steel or alloy steels. Precision casting is therefore the highest quality casting on the market today.
Molding and time are also costs associated with precision casting. When producing a casting, a mold and wax pattern are required. Both require more time and money. The process is therefore not cost-effective for small quantities.
What is Precision Casting Processes
Step 1. MOLD DESIGN
The mold design will be completed as per the drawing by our engineer. A mold is purchased from a mold manufacturer.
Step 2. WAX INJECTION
Wax is being injected by a machine. An injection molding machine produces wax designs of the desired castings. This process is called patterns.
Step 3 . ASSEMBLY TREE
To form a casting cluster or assembly tree, the patterns are attached to a central wax stick, called a sprue.
Step 4. SHELL MAKING
In order to build the shell, the assembly is immersed in a liquid ceramic slurry and then into a bed of extremely fine sand. This process may be repeated six times. As it dries between layers, the shell is complete.
Step 5. DEWAX
After the ceramic has dried, it is heated. Wax is melted from the ceramic. The wax will flow out of the ceramic shell.
Step 6. CASTING
Shells are filled with molten metal by gravity pouring in the conventional process. Casting becomes solid once the metal cools, and the parts and gates, sprue, and pouring cup become solid.
Step 7. KNOCKOUT
By vibration or a knock-out machine, the ceramic shell will be broken off when the metal has cooled and solidified.
Step 8. CUT OFF
A high-speed friction saw is used to cut away the parts from the central spruce.
Step 9. GRINDING
Castings are cut off after they are drilled. The pouring part of the casting is ground carefully.
Step 10.Inspection and Post Treatment.
As per the drawing and quality request, the casting will be inspected by an inspector. This will be the case if there are any unqualified parts. A second inspection and repair will be performed.
Step 11. FINISHED CASTINGS
Metal castings are ready for shipment to the customer after surface finishing operations are completed.
WHY CASTINGS FROM CIREX
CIREX is your reliable partner in precision investment castings and strongly values a good client relationship. We would like to be a development partner with you, sharing our thoughts and ideas about product design, material choice, measurements, and machining with you.
All of this is customized to your specifications. Taking a joint approach to casting is our general principle. A project’s success depends on the extent of co-development. For further details and contact please visit their official website
here.